Our research group has been studying control valves for more than ten years. Thanks to the collaboration with national and international companies, our group can rely on an extended practical experience on hydraulic devices.
Several approaches are used to address the research:
- Numerical analysis through CFD methods;
- Experimental investigations using the Hydraulic Laboratory facilities;
- Conceptual and theoretical analysis.
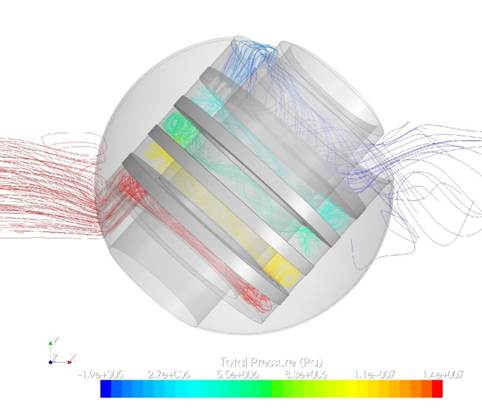
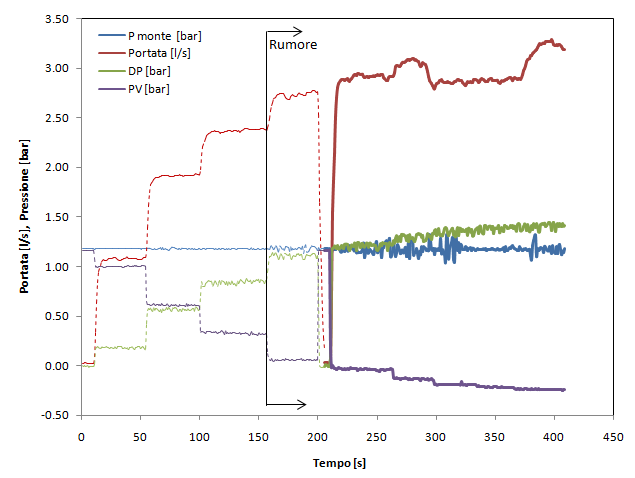
The research group designed and realized test plants for both compressible and incompressible fluids for standard devices characterization and research. Together with the experimental tests, numerical analysis through CFD methods has been adopted to fully characterize control devices, extending the experimental data to a wide range of applications. Moreover, using the experimental data to validate the numerical model, CFD permitted us to study particularly complex problems and develop new methods to predict crucial parameters of the devices.
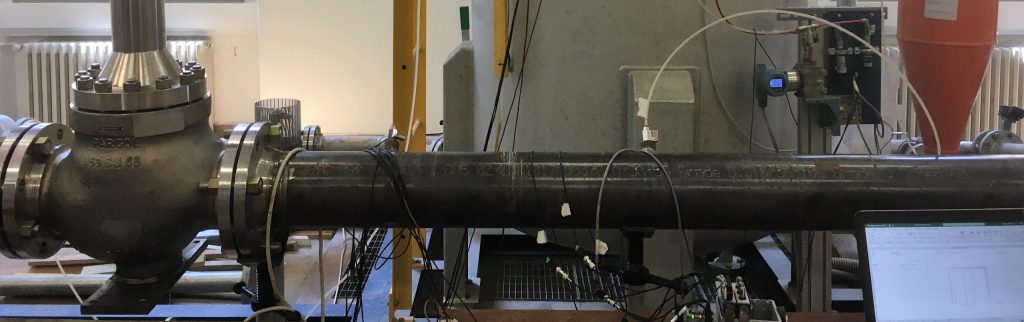
Fluid Dynamic Characterization
Control valves are devices used to regulate liquid, gas and multiphase flows, controlling specific parameters, such as flow rate, pressure drop and temperature.
On these devices, our research group performs numerical analysis through computational fluid dynamics technics in order to fully characterize their behavior and calculate the efficiency and other parameters used for their application.
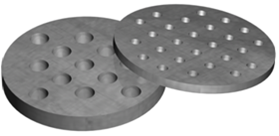
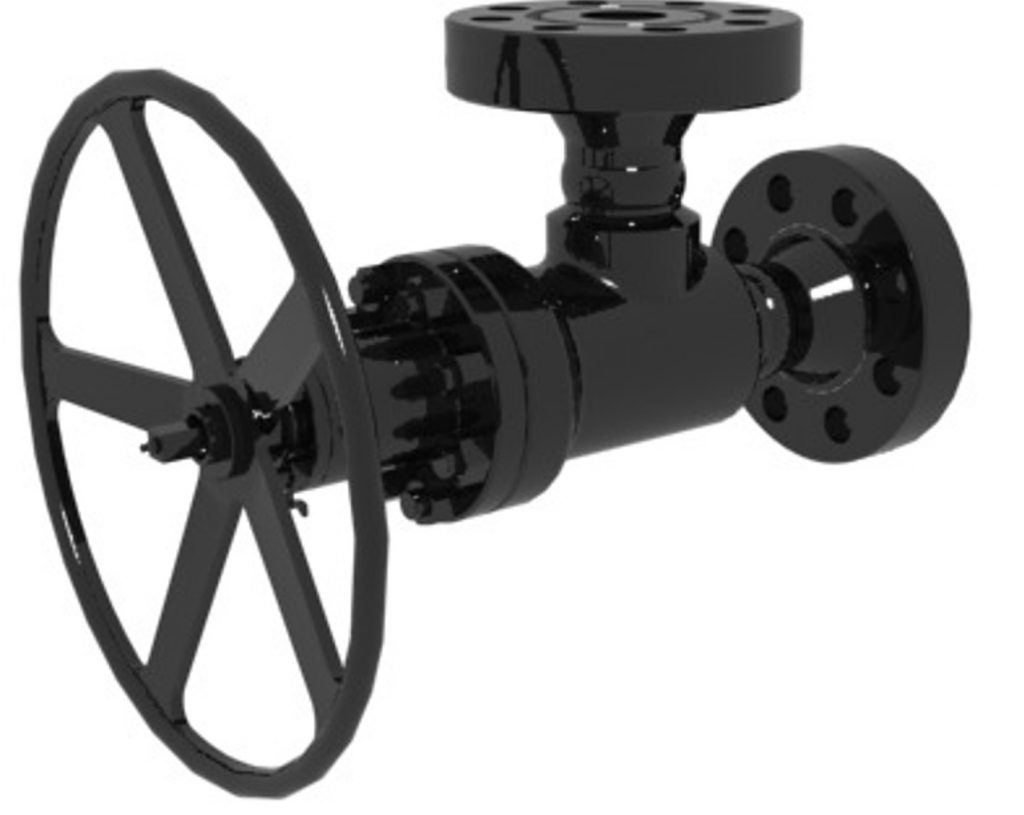
The numerical study is complementary to the tests conducted in Fantoli laboratory (Hydraulic Lab G. Fantoli), where a test plant, designed and realized according to the international standards, is available in the control valves section both for research activities and external commissions.
plotThe synergy between experimentation and numerical analysis allows to exhaustively and accurately study the characteristics of many different hydraulic devices, calculating the parameters defined in IEC and ISA standards. The characterization of one device is often followed by a phase of optimization and development of new applicative solutions.
An example of research, where both experimental and numerical studies have been necessary, regards cavitation, a harmful phenomenon for control valves that starting from noise and vibration can bring erosion and pitting of mechanical parts. Our aim has been the development of a method to predict the incipient cavitation number, a parameter that identifies the onset of cavitation, through single-phase flow simulations.
The experimental data have been used to validate the new numerical method and extend its applicability to a wide range of hydraulic devices, such as control valves, orifices, perforated plates, quick connector.